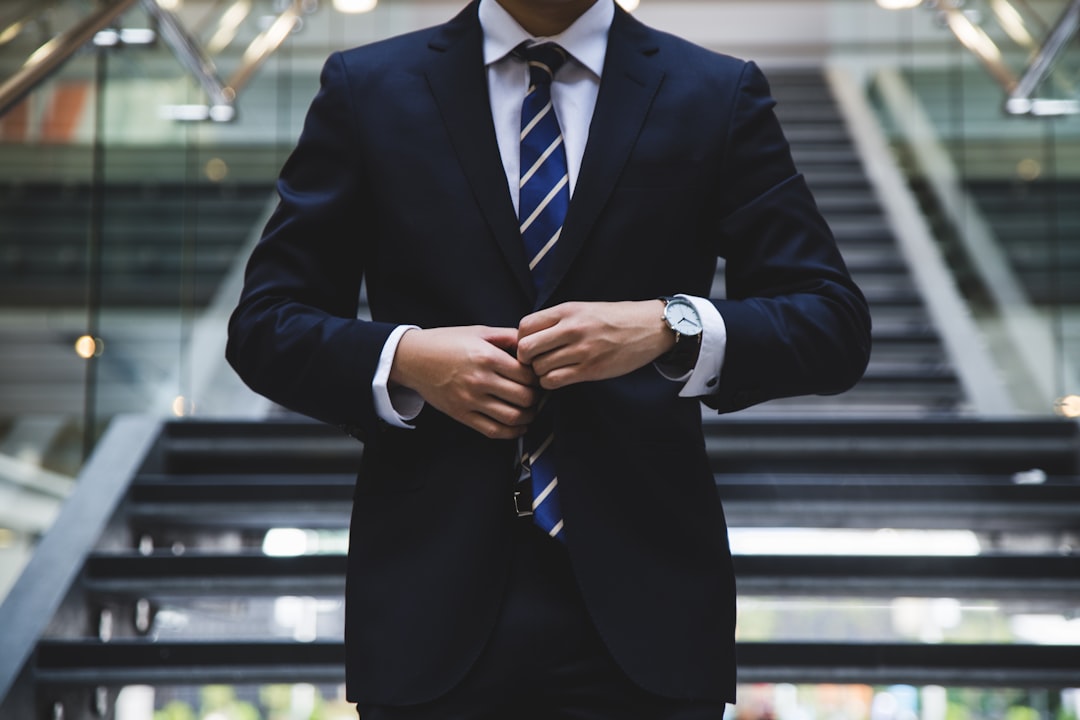
How to Optimize Operational Efficiency: Key Strategies for Business Growth
# Introduction. In today's competitive business landscape, operational efficiency has become a critical factor for success. Companies that optimize their processes not only reduce costs but also enhance productivity, leading to increased profitability and customer satisfaction. This blog post will explore effective strategies to optimize operational efficiency, enabling businesses to thrive in their respective markets. # Understand Your Current Processes. Before you can improve your operational efficiency, it is essential to understand your existing processes thoroughly. Start by mapping out your workflows, identifying each step and its purpose. Engage employees in this assessment, as they can offer invaluable insights into the challenges they face daily. By gaining a clear understanding of your operations, you can pinpoint inefficiencies and areas that require improvement. # Implement Lean Principles. Lean principles focus on maximizing value while minimizing waste. Adopting strategies such as Just-In-Time (JIT) production, where products are made only as needed, can significantly enhance efficiency. Additionally, consider techniques like value stream mapping to visualize and analyze your processes systematically. This strategic approach will help eliminate non-value-adding activities, thereby streamlining operations and improving overall efficiency. # Invest in Technology. In the digital age, leveraging technology is essential for achieving operational efficiency. Implementing software solutions for project management, inventory control, and customer relationship management can facilitate real-time information sharing and enhance communication within teams. Automation of repetitive tasks allows your workforce to focus on higher-level activities that drive innovation and growth. Evaluate your current technology stack and seek tools that align with your business objectives. # Foster a Culture of Continuous Improvement. Creating a culture of continuous improvement encourages employees to identify inefficiencies and suggest solutions proactively. Establish regular feedback loops, facilitate training sessions, and provide recognition for innovative ideas. Techniques such as Six Sigma can aid in this process by using data-driven approaches to refine operations. Engaging employees in improving processes not only fosters a positive workplace culture but also enhances productivity. # Monitor Key Performance Indicators (KPIs). To optimize operational efficiency, businesses need to define and monitor key performance indicators (KPIs) that reflect their operational performance. These metrics can include production costs, turnaround time, customer satisfaction rates, and employee productivity. By continuously tracking these KPIs, businesses can gain actionable insights into their operations, enabling data-driven decision-making. Adjustments can then be made to optimize processes based on these insights. # Streamline Communication. Effective communication is crucial for operational efficiency. Ensure that information flows seamlessly among departments through proper channels and collaboration tools. Regularly scheduled meetings and updates can help keep everyone on the same page and encourage collective problem-solving. Establishing clear communication protocols reduces misunderstandings and enhances teamwork, ultimately streamlining operations and improving efficiency. # Conclusion. Optimizing operational efficiency is a multidimensional approach that requires assessing existing processes, embracing technology, fostering a culture of improvement, and monitoring key performance indicators. By implementing the strategies discussed in this article, businesses can enhance their efficiency, ultimately leading to increased growth and success. The road to operational efficiency is ongoing, and consistent evaluation will help your business adapt and thrive in a rapidly changing environment. .